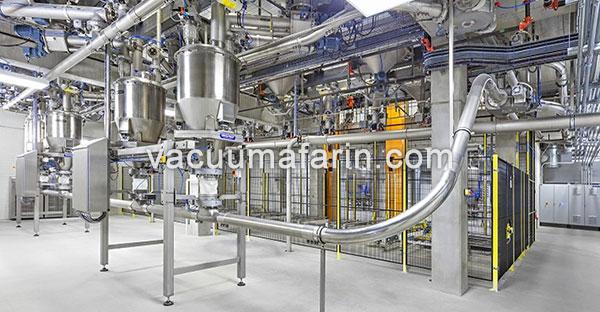
مقدمه
انتقال مواد پودری با سيستم وكيوم در صنايع معدنی و فلزات هم بسیار متداول است سیستم انتقال مواد باروش وکیوم برای موادمعدنی (ازقبیل سیمان، آهک و..) بصورت کاملا ایمن صورت می گیردو از نشتی گرد وغبار این مواد به خارج از دستگاه جلوگیری می شود. دراین روش بدلیل سیستم کاملا بسته انتقال مواد از هرگونه آلودگی محیطی جلوگیری می شود وبدلیل اینکه سایز واندازه گرد وغباراین مواد معدنی معمولابسیارکوچک ودراندازه های میکرونیزه می باشد بهمین دلیل باعث آلوده شدن هوای قابل تنفس نیروی انسانی می باشد. درحال حاضر ادارات محیط زیست برای جلوگیری از آسیب دیدن نیروهای انسانی درمحیط آلوده این سیستم وکیوم را جهت تایید ایمن کار پیشنهاد می دهد.
مزيت استفاده از سيستم وكيوم براي انتقال مواد پودری فلزی معدنی
انتقال مواد پودری به روش وکیوم و پنوماتیک به یکی از محبوب ترین روش های حمل و نقل برای طیف گسترده ای از مواد دارویی ، مواد مغذی و غذایی تبدیل شده است. استفاده بهینه از روش خلاء در فازهای رقیق یا غلیظ ، تضمین می کند که پودر یا گرانول درون فرآیند باقی بماند ، درعوض سیستم های انتقال فشار مثبت باعث نشت مواد میکرونیزه درمحیط وتلفات مواد می گردند. استفاده از روش خلاء فاز رقیق یا غلیظ می تواند در طیف وسیعی از عملیات دارویی از جمله بارگیری بلندرها یامخلوط کن ها ، دستگاه های صاف کننده ، آسیاب ها ، پرکننده های کپسول ، پرس قرص و حتی کار با قرص و کپسول بدون آسیب رساندن به محصول نهایی اعمال شود.
علاوه بر این ،محدودیت های فضای محیط تولیدی نسبتاً کوچک در بسیاری از مجموعه های فرآوری دارویی ، اغلب چالشی در انتقال پودرها جهت مخلوط کردن آنها برای فرآیندهای دارویی ایجاد می کند. انتقال مواد به روش وکیوم و پنوماتیکی راه حلی برای این محدودیت های محیطی ارائه می دهد.
انتقال مواد پودری به روش وکیوم و پنوماتیکی به یکی از محبوب ترین روش های حمل و نقل برای طیف گسترده ای از مواد دارویی ، مواد مغذی و غذایی تبدیل شده است
افزودنن سيستم وكيوم براي انتقال مواد پودری در فرآیندهای مختلف
عملیات انتقال مواد به روش خلاء اغلب می تواند مستقیماً در فرآیند ثانویه گنجانده شود تا تلاش برای اطمینان از عملکرد کاملا بسته و بدون نشتی ، بدون مواجهه اپراتور با محصول انجام شود. این فرایندهای اضافی شامل موارد زیر هستند: دستگاه تراش مخروطی خطی یا الک ؛ بارگیری مواد پودری قرص ؛ بارگیری / تخلیه گرانولاتورها ؛ تخلیه خشک کن های مایع؛ انتقال قرص / کپسول ؛ پر کردن مجدد فیدرها برای بارگذاری فرآیندهای مداوم مانند ایجاد دانه بندی ، مخلوط کردن ، آسیاب کردن یا میکرونیزاسیون و اکستروژن، انتقال مستقیم به فیدرها برای توزین دسته ای یا توزیع چندین نوع مواد مختلف در مخلوط كردن مواد به کار می رود.
طیف وسیعی از راه حل های انتقال مواد به روش خلاء دسته بندی شده و از پیش مهندسی شده برای کمک به فرایندهای تخلیه و شارژ مجدد ، که براساس یک انژکتور ونتوری یا یک پمپ خلاء الکتریکی ، طراحی شده است. سیستم هابا فاز متراکم را می توان با استفاده از سیستم های انتقال خلاء با کارایی بالا نیز تحقق بخشید. در فواصل کوتاه می توان از حالت انتقال فاز متراکم استفاده کرد.
انتقال مواد پودری به روش وکیوم در صنایع معدنی به عنوان روشی پذیرفته شده است
طراحی سيستم وكيوم براي انتقال مواد پودری باسازگاری بالا
طراحی یک سیستم مدولار فرصتی را برای انطباق سیستم وکیوم با تجهیزات مختلف فرآوری یا کنترلی رافراهم می کند.برای مثال چند نمونه از کاربردهارامی توان ذکر کرد ازقبیل تخلیه کیسه های ۲۵ کیلویی ، تخلیه درامها ، تخلیه کیسه های بزرگ جامبوبگ ، پر کردن مجدد فیدرها ، بارگیری راکتور که با استفاده از سیستمهای انتقال وکیوم یا خلاء با طراحی مهندسی جمع و جور و سبک صورت می پذیرد واین روش برای کاربردهای دستی یا اتوماتیک مناسب هستند.
مزايا سيستم وكيوم براي انتقال مواد پودری
• انتقال بدون گرد و غبار
• جلوگیری از هر گونه نشتي احتمالي در سيستم
• اتصال سيستم به منبع هواي فشرده با اجكتور ویا استفاده از پمپهای وکیوم باموتورهای الکتریکی
• مناسب برای استفاده در محیطهای منفجره وقابل احتراق
• انتقال با استاندارد بهداشتی
• تجهیزات جمع و جور و سبک وزن
• امكان انتقال مواد پودری به صورت بچ به بج و پیوسته
• امكان انتقال مواد پودري معدني با انواع و اقسام روش هاي مهندسي متنوع
انتقال مواد پودری با روش وکیوم در صنایع فلزات می تواند نتیجه بهتری داشته باشد
كاربردهای سيستم وكيوم براي انتقال مواد پودری
• پودرهای ریز و درشت ، گرانول ها و مواد حجیم ، قطعات کوچک
• انتقال حجم ۰.۱ تا ۸ مترمكعب در ساعت
• امكان انتقال مواد پودری تا ارتفاع حداكثر ۴۰ متر
• استفاده از تجهیزات اضافی مانند (مدارهای الکترونیک داخلی، جداکننده آهنربا، نیلبر)
• انتقال قرص و ذرات فشرده
• مخزن ذخیره برای پر کردن میکسر
• تغذیه مجدد فیدر ، هم حجمی و هم وزنی
• خطوط بسته بندي
مشخصات فنی سیستم وکیوم برای انتقال مواد پودری
• سیستم های ساخته شده از فولاد ضد زنگ ۳۰۴ و ۳۱۶
• مناسب انواع و اقسام صنایع از قبیل مواد غذایی تا مواد معدنی و فلزات
• مناسب مواد با خاصیت ساینده وخورنده
• الزام اجرای قوانین ایمنی کار
• تمیز کردن خودکار فیلتر در هنگام تخلیه مواد
در انتقال مواد پودری با سیستم وکیوم می توان تا ارتفاع ۴۰ متر می توان مواد را انتقال داد
اصول عملکرد سیستم وکیوم برای انتقال مواد پودری
اکثر سیستم های انتقال مواد پودری به روش ، بر اساس یک سیکل کاملی کار می کنند که در آن مواد برای مدت زمان مشخصی به یک سطح منتقل می شود ،سپس انتقال مواد پودری متوقف می شود ، دریچه تخلیه باز می شوند و فیلترها تمیز می شوند. . سپس این توالی تکرار می شود. انتقال مواد پودری در حالت پیوسته را می توان با استفاده از شیر دورانی در خروجی هاپر ذخیره مواد انجام داد.
این تجهیزات مواد را از طریق تجهیزات مختلفی از جمله لنس مکش یاتورچ انتقال مواد ، قیف های تغذیه ای ، اسکرو های تغذیه ای ، شیرهای دورانی ، اکسترودرها و … وارد خط انتقال می کنند .بدلیل اختلاف فشار ایجاد شده دردونقظه جریان مکش هوایا گاز توسط پمپهای وکیوم واقع در انتهای خط ، ایجاد می شود و بنابراین مواد از طریق خط لوله به هاپر وکیوم یا خلاء مکیده می شود. در یک مخزن خلا ، گاز با عبور از فیلتر که از مواد جامد عبور می کند ، از محصول جدا می شود. در طول هر سیکل تخلیه ، فیلتر با دمیدن هوای فشرده به طور خودکار تمیز می شود.
در انتقال مواد پودری به روش وکیوم می توان به راحتی و بدون نگرانی، مواد را انتقال داد
فرآوری مواد پودری معدنی با استفاده از سیستم وکیوم
فرآوری مواد ، مجموعه عملیاتی است که مواد صنعتی را از حالت مواد اولیه به قطعات یا محصولات نهایی تبدیل می کند. مواد صنعتی ، مانند ماشین آلات و تجهیزات کم و بیش با دوام تولید شده برای صنعت و مصرف کنندگان ،به عنوان موادی که در تولید کالاهای سخت استفاده می شود ، در مقایسه با کالاهای نرم یکبار مصرف ، مانند مواد شیمیایی ، مواد غذایی ، دارویی و پوشاک است.
فرآوری مواد بصورت دستی به قدمت یک تمدن است. مکانیزاسیون با انقلاب صنعتی قرن هجدهم آغاز شد و در اوایل قرن نوزدهم ماشین های اساسی برای شکل گیری ، شکل دادن و برش ، عمدتا در انگلستان توسعه یافت. از آن زمان ، روش ها ، تکنیک ها و ماشین آلات فرآوری مواد به تنوع و تعداد بیشتری رسیده اند.
سیکل فرآیندهای تولید که مواد را به قطعات و محصولات تبدیل می کند ، بلافاصله پس از استخراج مواد اولیه از مواد معدنی یا تولید مواد شیمیایی اولیه یا مواد طبیعی آغاز می شود. مواد اولیه فلزی معمولاً در دو مرحله تولید می شوند. ابتدا سنگ معدن خام فرآوری می شود تا غلظت فلز مورد نظر افزایش یابد. این را فراوری می نامند. فرآیندهای معمول شامل خرد کردن ، بو دادن ، جداسازی مغناطیسی ، شناور سازی و شستشو است. دوم ، فرآیندهای اضافی مانند ذوب و آلیاژ سازی برای تولید فلزی که قرار است به قطعات ساخته شود و در نهایت به یک محصول مونتاژ می شوند ، استفاده می شود.
در انتقال مواد پودری می توان مواد پودری را به دور ازگرد و غبار به محل مقصد منتقل کرد
فراوري مواد در مواد سراميكي و استفاده از سیستم وکیوم
در مورد مواد سرامیکی ، خاک رس طبیعی مخلوط شده و با سیلیکات های مختلف مخلوط می شود تا ماده اولیه تولید شود. رزین های پلاستیکی با روش های شیمیایی به صورت پودر ، گلوله ، بتونه یا مایع تولید می شوند. لاستیک مصنوعی همچنین با استفاده از تکنیک های شیمیایی ساخته می شود ، همانطور که لاستیک طبیعی ، به اشکال مانند اسلب ، ورق ، کرپ و کف برای ساخت قطعات نهایی تولید می شود.
فرایندهایی که برای تبدیل مواد اولیه به محصولات نهایی استفاده می شوند ، یک یا هر دو عملکرد اصلی را انجام می دهند: اول ، آنها مواد را به شکل دلخواه در می آورند. دوم ، آنها خصوصیات مواد را تغییر می دهند یا بهبود می بخشند.
فراوری مواد براي انتقال مواد پودری ممکن است برای اصلاح سطح مواد به منظور محافظت از مواد در برابر خرابی توسط خوردگی ، اکسیداسیون ، سایش مکانیکی یا تغییر شکل استفاده شود
فرایندهای شکل دهی و شکل گیری را می توان به دو نوع گسترده طبقه بندی کرد – آنهایی که روی مواد در حالت مایع انجام می شوند و آنهایی که روی مواد در شرایط جامد یا پلاستیک انجام می شوند. فرآوری مواد به صورت مایع معمولاً به عنوان ریخته گری شناخته می شود که شامل فلزات ، شیشه و سرامیک باشد. وقتی روی پلاستیک ها و برخی دیگر از مواد غیر فلزی اعمال می شود ، قالب نامیده می شود. بیشتر فرآیندهای ریخته گری و قالب ریزی شامل چهار مرحله عمده است: (۱) ساخت الگوی دقیق قطعه ، (۲) ساخت قالب از الگو ، (۳) ورود مایع به قالب و (۴) برداشتن قسمت سخت شده از قالب گاهی اوقات به یک عملیات اتمام نیاز است.
مواد در حالت جامد خود با اعمال نیرو یا فشار به شکل های دلخواه در می آیند. مواد مورد فرآوری می توانند در شرایط نسبتاً سخت و پایدار و در فرم هایی مانند میله ، ورق ، گلوله یا پودر قرار داشته باشند ، یا می توانند به صورت نرم ، پلاستیکی یا مانند خاکی باشند. مواد جامد را می توان گرم یا سرد تشکیل داد. فرآوری فلزات در حالت جامد را می توان به دو مرحله عمده تقسیم کرد: اول ، مواد اولیه به صورت شمش های بزرگ یا شمش های گرم کار می شود ، معمولاً با غلتک زدن ، جعل یا اکستروژن ، به شکل ها و اندازه های کوچکتر. دوم ، این اشکال توسط یک یا چند فرآیند گرم یا سرد به مقادیر نهایی و محصولات تبدیل می شوند.
نتيجه گيری
فراوری مواد براي انتقال مواد پودری ممکن است برای اصلاح سطح مواد به منظور محافظت از مواد در برابر خرابی توسط خوردگی ، اکسیداسیون ، سایش مکانیکی یا تغییر شکل استفاده شود. برای ایجاد ویژگی های خاص سطح مانند بازتابندگی ، رسانایی الکتریکی یا عایق بندی ، یا ویژگی های تحمل یا به مواد جلوه های تزئینی خاصی می بخشد. دو گروه گسترده از فرایندهای اتمام وجود دارد ، آنهایی که در آن یک پوشش ، معمولاً از ماده ای متفاوت ، روی سطح قرار می گیرد و آنهایی که در آن سطح ماده با اثر شیمیایی ، گرما یا نیروی مکانیکی تغییر می کند. گروه اول شامل پوشش فلزی مانند آبکاری است. فراوري ارگانیک ، مانند رنگ آميزی ؛ و میناکاری چینی.